Электроэрозионная обработка

Электроэрозионная обработка ( ЭЭО ), также известная как искровая обработка , искровая эрозия , штамповка , сжигание проволоки или эрозия проволоки , представляет собой металлпроцесс изготовления, при котором желаемая форма достигается с помощью электрических разрядов (искры). [1] Материал удаляется из заготовки серией быстро повторяющихся разрядов тока между двумя электродами , разделенными диэлектрической жидкостью и находящимися под действием электрического напряжения . Один из электродов называется электродом-инструментом или просто инструментом или электродом , а другой называется электродом-заготовкой или заготовкой . Процесс зависит от того, что инструмент и заготовка не вступают в физический контакт. Чрезвычайно твердые материалы, такие как карбиды, керамика, титановые сплавы и термообработанные инструментальные стали, которые очень трудно обрабатывать обычным способом, можно точно обрабатывать с помощью электроэрозионной обработки. [2]
Когда напряжение между двумя электродами увеличивается, напряженность электрического поля в пространстве между электродами становится больше, вызывая диэлектрический пробой жидкости и образуя электрическую дугу. В результате материал удаляется с электродов. После прекращения тока (или его прекращения в зависимости от типа генератора) в межэлектродный объем подается новый жидкий диэлектрик, что позволяет унести твердые частицы (мусор) и восстановить изоляционные свойства диэлектрика. . Добавление нового жидкого диэлектрика в межэлектродный объем принято называть промывкой . После протекания тока напряжение между электродами восстанавливается до того значения, которое было до пробоя, так что может произойти новый пробой жидкого диэлектрика, повторяющий цикл.
История [ править ]
Эрозионное действие электрических разрядов впервые было отмечено в 1770 году английским физиком Джозефом Пристли .
Электроэрозионный электроэрозионный станок [ править ]
Двум советским ученым — Б. Р. Лазаренко и Н. И. Лазаренко — в 1943 г. было поручено исследовать способы предотвращения эрозии вольфрамовых электрических контактов вследствие искрения. Им не удалось справиться с этой задачей, но они обнаружили, что эрозия контролировалась более точно, если электроды были погружены в диэлектрическую жидкость. Это побудило их изобрести электроэрозионный станок, используемый для обработки труднообрабатываемых материалов, таких как вольфрам. Машина Лазаренко известна как машина RC-типа, по названию цепи резистор-конденсатор (RC-цепь), используемой для зарядки электродов. [3] [4] [5] [6]
Одновременно, но независимо, американская группа Гарольда Старка, Виктора Хардинга и Джека Бивера разработала электроэрозионный станок для удаления сломанных сверл и метчиков из алюминиевых отливок. [7] Первоначально создавая свои машины из электротравильных инструментов с недостаточной мощностью, они не добились большого успеха. Но более мощные искровые устройства в сочетании с автоматическим повторением искры и заменой жидкости с помощью электромагнитного прерывателя позволили создать практичные машины. Машины Старка, Хардинга и Бивера производили 60 искр в секунду. Более поздние машины, основанные на их конструкции, использовали схемы с вакуумными лампами , которые производили тысячи искр в секунду, что значительно увеличивало скорость резки. [8]
Проволочная электроэрозионная обработка [ править ]
Проволочный тип станка возник в 1960-х годах для изготовления инструментов ( матриц ) из закаленной стали. Электрод-инструмент в проволочной электроэрозионной обработке представляет собой просто проволоку. Чтобы избежать эрозии проволоки, приводящей к ее обрыву, проволоку наматывают между двумя катушками, так что активная часть проволоки постоянно меняется. Самые ранние станки с числовым программным управлением (NC) представляли собой модификацию вертикальных фрезерных станков с перфолентой. Первый коммерчески доступный станок с ЧПУ, выполненный в виде проволочно-эрозионного станка, был изготовлен в СССР в 1967 году. Машины, которые могли оптически следовать линиям на мастер-чертеже, были разработаны группой Дэвида Х. Дулебона в 1960-х годах в компании Эндрю Инжиниринг. [9] для фрезерных и шлифовальных станков. Мастер-чертежи позже были созданы на плоттерах с числовым программным управлением (ЧПУ) для большей точности. В 1974 году был произведен проволочный электроэрозионный станок с использованием волочильного плоттера с ЧПУ и оптического отслеживания линий. Позже Дулебон использовал ту же программу с ЧПУ для плоттера для непосредственного управления электроэрозионным станком, и первый электроэрозионный станок с ЧПУ был произведен в 1976 году. [10]
Возможности и использование коммерческой электроэрозионной обработки проволоки существенно расширились за последние десятилетия. [11] Скорость подачи увеличилась [11] качество поверхности можно точно контролировать. [11]
Общие сведения [ править ]

Электроэрозионная обработка — это метод обработки, в основном используемый для твердых металлов или тех металлов, которые было бы очень трудно обрабатывать традиционными методами. Электроэрозионная обработка обычно работает с электропроводящими материалами, хотя также были предложены методы использования электроэрозионной обработки для обработки изолирующей керамики . [12] [13] Электроэрозионная обработка позволяет вырезать сложные контуры или полости в предварительно закаленной стали без необходимости термической обработки для их смягчения и повторного упрочнения. Этот метод можно использовать с любым другим металлом или металлическим сплавом, таким как титан , хастеллой , ковар и инконель . о применении этого процесса для формирования поликристаллических алмазных инструментов. Также сообщалось [14]
Электроэрозионную обработку часто включают в «нетрадиционную» или «нетрадиционную» группу методов обработки вместе с такими процессами, как электрохимическая обработка (ECM), водоструйная резка (WJ, AWJ), лазерная резка и противоположные «традиционным» методам обработки. «группа ( точение , фрезерование , шлифование , сверление и любой другой процесс, механизм удаления материала которого по существу основан на механических силах). [15]
В идеале электроэрозионную обработку можно рассматривать как серию пробой-восстановление жидкого диэлектрика между электродами. Однако следует проявлять осторожность при рассмотрении такого утверждения, поскольку оно представляет собой идеализированную модель процесса, введенную для описания фундаментальных идей, лежащих в основе процесса. Тем не менее, любое практическое применение включает в себя множество аспектов, которые, возможно, также необходимо учитывать. Например, удаление мусора из межэлектродного объема, скорее всего, всегда будет частичным. При этом электрические свойства диэлектрика в межэлектродном объеме могут отличаться от их номинальных значений и даже изменяться со временем. Межэлектродное расстояние, часто называемое еще искровым зазором, является результатом алгоритмов управления конкретной используемой машины. Контроль такой дистанции логически представляется центральным в этом процессе. Кроме того, не весь ток между диэлектриком относится к идеальному типу, описанному выше: искровой промежуток может быть закорочен обломками. Система управления электродом может не среагировать достаточно быстро, чтобы предотвратить контакт двух электродов (инструмента и заготовки) с последующим коротким замыканием. Это нежелательно, поскольку короткое замыкание способствует удалению материала иначе, чем в идеальном случае. Промывочное действие может быть недостаточным для восстановления изолирующих свойств диэлектрика, так что ток всегда возникает в точке межэлектродного объема (это называется искрением) с последующим нежелательным изменением формы (повреждением) диэлектрика. инструмент-электрод и заготовка. В конечном счете, описание этого процесса подходящим способом для конкретной цели — это то, что делает область EDM таким богатым полем для дальнейших исследований и исследований. [16]
Для получения определенной геометрии электроэрозионный инструмент направляется по желаемой траектории очень близко к детали; в идеале он не должен касаться заготовки, хотя на самом деле это может произойти из-за особенностей используемого конкретного управления движением. Таким образом, происходит большое количество разрядов тока (в просторечии также называемых искрами), каждый из которых способствует удалению материала как с инструмента, так и с заготовки, где образуются небольшие кратеры. Размер кратеров зависит от технологических параметров, заданных для конкретной работы. Они могут иметь типичные размеры от наноразмеров (при микроэрозионных операциях) до нескольких сотен микрометров в условиях черновой обработки.
Наличие этих небольших кратеров на инструменте приводит к постепенной эрозии электрода. Эту эрозию инструмента-электрода также называют износом. Необходимы стратегии, позволяющие противодействовать вредному влиянию износа на геометрию заготовки. Одной из возможностей является непрерывная замена электрода-инструмента во время операции механической обработки. Вот что происходит, если в качестве электрода использовать постоянно заменяемую проволоку. В этом случае соответствующий процесс электроэрозионной обработки также называется электроэрозионной проволокой. Электрод-инструмент также можно использовать таким образом, чтобы в процессе обработки фактически участвовала лишь небольшая его часть, и эта часть регулярно менялась. Так обстоит дело, например, при использовании вращающегося диска в качестве электрода-инструмента. Соответствующий процесс часто еще называют электроэрозионным шлифованием. [17]
Дальнейшая стратегия заключается в использовании набора электродов разных размеров и форм в ходе одной и той же операции электроэрозионной обработки. Это часто называют стратегией нескольких электродов, и она наиболее распространена, когда электрод-инструмент повторяет желаемую форму в отрицательном направлении и продвигается к заготовке в одном направлении, обычно вертикальном направлении (т.е. оси Z). Это напоминает погружение инструмента в диэлектрическую жидкость, в которую погружена заготовка, поэтому неудивительно, что его часто называют штамповочным электроэрозионным электроэрозионным станком (также называемым обычным электроэрозионным электроэрозионным станком и плунжерным электроэрозионным электроэрозионным станком). Соответствующие станки часто называют электроэрозионными станками. Обычно электроды этого типа имеют достаточно сложную форму. Если окончательная геометрия получается с использованием электрода обычно простой формы, который перемещается в нескольких направлениях и, возможно, также подвергается вращениям, часто используется термин электроэрозионное фрезерование. [18]
В любом случае степень износа строго зависит от технологических параметров, используемых при эксплуатации (например: полярности, максимального тока, напряжения холостого хода). Например, в микроэрозионной электроэрозионной обработке, также известной как микроэрозионная обработка, эти параметры обычно устанавливаются на значения, которые вызывают сильный износ. Поэтому износ является серьезной проблемой в этой области.
Решается проблема износа графитовых электродов. В одном из подходов цифровой генератор, управляемый в течение миллисекунд, меняет полярность во время электроэрозии. Это дает эффект, аналогичный гальванике, при котором эродированный графит постоянно откладывается обратно на электрод. В другом методе так называемая схема «нулевого износа» уменьшает частоту запуска и остановки разряда, сохраняя его как можно дольше. [19]
Определение технологических параметров [ править ]
Трудности возникли при определении технологических параметров, управляющих процессом.
На имеющихся в продаже электроэрозионных станках используются две широкие категории генераторов, также известных как источники питания: группа на основе RC-цепей и группа на основе импульсов, управляемых транзисторами .
В обеих категориях основными параметрами при настройке являются подаваемый ток и частота. Однако в RC-цепях ожидается небольшой контроль над продолжительностью разряда, которая, вероятно, будет зависеть от фактического состояния искрового промежутка (размера и загрязнения) в момент разряда. [20] Кроме того, напряжение холостого хода (т.е. напряжение между электродами, когда диэлектрик еще не разрушен) можно идентифицировать как установившееся напряжение RC-цепи.
В генераторах, основанных на транзисторном управлении, пользователь обычно может подать на электроды последовательность импульсов напряжения. Каждому импульсу можно задать форму, например квазипрямоугольную. В частности, можно установить время между двумя последовательными импульсами и длительность каждого импульса. Амплитуда каждого импульса представляет собой напряжение холостого хода. Таким образом, максимальная длительность разряда равна длительности импульса напряжения в шлейфе. Тогда ожидается, что два импульса тока не возникнут в течение продолжительности, равной или превышающей временной интервал между двумя последовательными импульсами напряжения.
Максимальный ток во время разряда, который выдает генератор, также можно контролировать. Поскольку разные производители машин могут использовать и другие типы генераторов, параметры, которые фактически могут быть установлены на конкретной машине, будут зависеть от производителя генератора. Детали генераторов и систем управления их машинами не всегда легко доступны пользователю. Это является барьером для однозначного описания технологических параметров процесса электроэрозионной обработки. При этом к регулятору движения электродов относятся и параметры, влияющие на явления, происходящие между инструментом и электродом.
Схема для определения и измерения электрических параметров во время операции электроэрозионной обработки непосредственно в межэлектродном объеме с помощью внешнего по отношению к машине осциллографа была недавно предложена Ферри и др. [21] Эти авторы проводили свои исследования в области микроэрозионной обработки, но тот же подход можно использовать в любой операции электроэрозионной обработки. Это позволит пользователю напрямую оценить электрические параметры, влияющие на его работу, не полагаясь на заявления производителя машины. При обработке разных материалов в одних и тех же условиях наладки реальные электрические параметры процесса существенно различаются. [21]
Механизм удаления материала [ править ]
Первая серьезная попытка дать физическое объяснение удаления материала при электроэрозионной обработке принадлежит, пожалуй, Ван Дейку. [22] Ван Дейк представил тепловую модель вместе с компьютерным моделированием, чтобы объяснить явления между электродами во время электроэрозионной обработки. Однако, как признал в своем исследовании сам Ван Дейк, количество предположений, сделанных для преодоления недостатка экспериментальных данных в то время, было весьма значительным.
Дальнейшие модели того, что происходит во время электроэрозионной обработки с точки зрения теплопередачи, были разработаны в конце восьмидесятых и начале девяностых годов. Результатом стали три научные статьи: первая представляет тепловую модель удаления материала на катоде, [23] второй представляет тепловую модель эрозии, происходящей на аноде. [24] третий представляет модель, описывающую плазменный канал, образующийся при прохождении разрядного тока через диэлектрическую жидкость. [25] Валидация этих моделей подтверждается экспериментальными данными, предоставленными AGIE.
Эти модели наиболее авторитетно подтверждают утверждение о том, что электроэрозионная обработка представляет собой термический процесс удаления материала с двух электродов в результате плавления или испарения, а также динамики давления, устанавливаемой в искровом промежутке в результате сжатия плазменного канала. Однако для малых энергий разряда модели недостаточны для объяснения экспериментальных данных. Все эти модели основаны на ряде предположений из таких разрозненных областей исследований, как взрывы подводных лодок, разряды газов и отказы трансформаторов, поэтому неудивительно, что совсем недавно в литературе были предложены альтернативные модели, пытающиеся объяснить процесс EDM.
Среди них модель от Сингха и Гоша. [26] связывает удаление материала с электрода с наличием электрической силы на поверхности электрода, которая может механически удалить материал и создать кратеры. Это стало бы возможным, поскольку материал на поверхности изменил механические свойства из-за повышения температуры, вызванного прохождением электрического тока. Моделирование авторов показало, как они могут объяснить электроэрозионную обработку лучше, чем тепловая модель (плавление или испарение), особенно для небольших энергий разряда, которые обычно используются в микроэрозионной электроэрозионной обработке и в операциях чистовой обработки.
Учитывая множество доступных моделей, похоже, что механизм удаления материала при электроэрозионной обработке еще недостаточно изучен и для его выяснения необходимы дальнейшие исследования. [21] особенно учитывая отсутствие экспериментальных научных данных для построения и проверки текущих моделей EDM. [21] Это объясняет увеличение текущих исследовательских усилий в области соответствующих экспериментальных методов. [16]
Типы [ править ]
Грузило EDM [ править ]
Электроэрозионная обработка с погружением, также называемая плунжерной электроэрозионной электроэрозией, полой электроэрозионной обработки или объемной электроэрозионной обработки, состоит из электрода и заготовки, погруженных в изолирующую жидкость, например, чаще всего, в изолирующую жидкость. [28] масло или, реже, другие диэлектрические жидкости. Электрод и заготовка подключаются к подходящему источнику питания. Источник питания создает электрический потенциал между двумя частями. При приближении электрода к заготовке в жидкости происходит пробой диэлектрика, образующий плазменный канал, [16] [23] [24] [25] и проскакивает маленькая искра.
Эти искры обычно выскакивают по одной, [28] поскольку очень маловероятно, чтобы разные места в межэлектродном пространстве имели одинаковые локальные электрические характеристики, которые позволили бы искре возникнуть одновременно во всех таких местах. Эти искры возникают в огромных количествах в, казалось бы, случайных местах между электродом и заготовкой. По мере эрозии основного металла и последующего увеличения искрового промежутка машина автоматически опускает электрод, чтобы процесс мог продолжаться непрерывно. В секунду возникает несколько сотен тысяч искр, при этом фактический рабочий цикл тщательно контролируется параметрами настройки. Эти циклы управления иногда называют «время включения» и «время отключения», которые в литературе имеют более формальное определение. [16] [21] [29]
Настройка времени включения определяет длину или продолжительность искры. Следовательно, чем дольше время работы, тем глубже образуется впадина от каждой искры, что приводит к более грубой обработке заготовки. Обратное верно для более коротких сроков. Время выключения — это период времени между искрами. Хотя это время не влияет напрямую на обработку детали, время простоя позволяет промывать диэлектрическую жидкость через сопло для очистки эрозионного мусора. Недостаточное удаление мусора может привести к повторным ударам в одном и том же месте, что может привести к короткому замыканию. Современные контроллеры контролируют характеристики дуг и могут изменять параметры за микросекунды для компенсации. Типичная геометрия детали представляет собой сложную трехмерную форму. [28] часто с небольшими углами или углами странной формы. Также используются вертикальные, орбитальные, векторные, направленные, винтовые, конические, вращательные, вращательные и индексирующие циклы обработки.
Электроэрозионная обработка проволоки [ править ]


При электроэрозионной обработке проволоки (WEDM), также известной как электроэрозионная резка проволоки и резка проволоки , [30] тонкая одножильная металлическая проволока, обычно латунная , проходит через заготовку, погруженную в резервуар с диэлектрической жидкостью, обычно деионизированной водой. [28] Электроэрозионная обработка проволокой обычно используется для резки листов толщиной до 300 мм, а также для изготовления пуансонов, инструментов и штампов из твердых металлов, которые трудно обрабатывать другими методами.
Проволока, постоянно подаваемая с катушки, удерживается между верхней и нижней алмазными направляющими, центрированными в головке водяного сопла. Направляющие, обычно управляемые ЧПУ , перемещаются в плоскости x – y . На большинстве станков верхняя направляющая также может перемещаться независимо по осям z – u – v , что дает возможность резать конические и переходные формы (например, круг внизу, квадрат вверху). Верхняя направляющая может управлять перемещениями осей в стандарте GCode, x – y – u – v – i – j – k – l –. Это позволяет запрограммировать электроэрозионный станок для резки очень сложных и деликатных форм.
Верхняя и нижняя алмазные направляющие обычно имеют точность до 0,004 мм (0,16 мил) и могут иметь траекторию резания или пропил всего 0,021 мм (0,83 мил) при использовании проволоки диаметром 0,02 мм (0,79 мил), хотя средний размер пропила обеспечивает наилучшую экономичность и время обработки 0,335 мм (13,2 мил) при использовании латунной проволоки диаметром 0,25 мм (9,8 мил). Причина, по которой ширина резки превышает ширину проволоки, заключается в том, что искрение возникает по краям проволоки к заготовке, вызывая эрозию. [28] Этот «перерез» необходим, для многих применений он достаточно предсказуем и, следовательно, может быть компенсирован (например, в микроэрозионной обработке это случается нечасто). Катушки с проволокой длинные — 8-килограммовая катушка с проволокой 0,25 мм имеет длину чуть более 19 километров. Диаметр проволоки может составлять всего 20 мкм (0,79 мил), а точность геометрии составляет около ± 1 мкм (0,039 мил).
В процессе резки проволоки в качестве диэлектрической жидкости используется вода, а ее удельное сопротивление и другие электрические свойства контролируются с помощью фильтров и с ПИД-управлением деионизаторов . Вода смывает остатки резки из зоны резки. Промывка является важным фактором при определении максимальной скорости подачи для заданной толщины материала.
Помимо более жестких допусков, многоосные электроэрозионные обрабатывающие центры для резки проволоки имеют дополнительные функции, такие как несколько головок для одновременной резки двух деталей, элементы управления для предотвращения обрыва проволоки, функции автоматического самозарезания резьбы в случае обрыва проволоки и программируемые стратегии обработки. оптимизировать работу.
Электроэрозионная обработка проволокой обычно используется, когда желательны низкие остаточные напряжения, поскольку для удаления материала не требуются высокие силы резания. Если энергия импульса относительно невелика (как при чистовых операциях), ожидается небольшое изменение механических свойств материала из-за этих низких остаточных напряжений, хотя материал, который не был снят с напряжения, может деформироваться в процессе обработки.
Заготовка может подвергаться значительному термическому циклу, степень его тяжести зависит от используемых технологических параметров. Такие термические циклы могут вызвать образование повторно отлитого слоя на детали и остаточных растягивающих напряжений на заготовке. Если механическая обработка проводится после термообработки, на точность размеров не повлияет искажение от термообработки. [31]
Электроэрозионный станок для быстрого сверления [ править ]
Электроэрозионный станок для быстрого сверления отверстий был разработан для быстрого, точного изготовления небольших и глубоких отверстий. Концептуально это похоже на электроэрозионную обработку с грузилом, но электрод представляет собой вращающуюся трубку, по которой подается струя диэлектрической жидкости под давлением. Он может проделать отверстие глубиной в дюйм примерно за минуту и является хорошим способом обработки отверстий в материалах, слишком твердых для обработки спиральным сверлом. Этот тип электроэрозионного сверления широко используется в аэрокосмической промышленности для создания охлаждающих отверстий в лопастях и других компонентах авиационных систем. Он также используется для сверления отверстий в лопатках промышленных газовых турбин, в формах и штампах, а также в подшипниках.
Приложения [ править ]
Производство прототипов [ править ]
Процесс электроэрозионной обработки наиболее широко используется в производстве пресс-форм, инструментов и штампов , но становится распространенным методом изготовления прототипов и серийных деталей, особенно в аэрокосмической, автомобильной и электронной промышленности, где объемы производства относительно невелики. В электроэрозионном станке графитовому , медно-вольфрамовому или чисто медному электроду придается желаемая (отрицательная) форма и подается в заготовку на конце вертикального плунжера.
Изготовление штампов для монет [ править ]
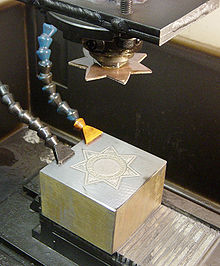
Для изготовления штампов для изготовления ювелирных изделий и значков или вырубки и прошивки (с использованием блинной матрицы ) методом чеканки (штамповки) позитивный мастер может быть изготовлен из серебра 925 пробы, поскольку (при соответствующих настройках станка) мастер значительно размыт и используется только один раз. Полученную отрицательную матрицу затем закаливают и используют с помощью молотка для изготовления штампованных лысок из вырезанных листовых заготовок из бронзы, серебра или низкопробного золотого сплава. Для значков этим плоскостям можно дополнительно придать изогнутую поверхность с помощью другого штампа. Этот тип электроэрозионной обработки обычно выполняется погруженным в диэлектрик на масляной основе. Готовый объект может быть дополнительно усовершенствован путем нанесения твердой (стекло) или мягкой (краска) эмали или гальванического покрытия чистым золотом или никелем. На более мягких материалах, таких как серебро, в качестве изысканности можно выгравировать вручную.

Сверление небольших отверстий [ править ]


Электроэрозионный станок для сверления небольших отверстий используется в различных областях.
На электроэрозионных станках электроэрозионный станок для сверления небольших отверстий используется для проделывания сквозного отверстия в заготовке, через которое можно продеть проволоку для операции электроэрозионной резки. Отдельная электроэрозионная головка, специально предназначенная для сверления небольших отверстий, устанавливается на проволочном станке и позволяет при необходимости и без предварительного сверления производить эродирование из больших закаленных пластин готовых деталей.
Электроэрозионная обработка малых отверстий используется для сверления рядов отверстий в передней и задней кромках турбинных лопаток, используемых в реактивных двигателях . Поток газа через эти маленькие отверстия позволяет двигателям использовать более высокие температуры, чем это возможно в противном случае. Высокотемпературные, очень твердые монокристаллические сплавы, используемые в этих лопастях, делают традиционную обработку этих отверстий с высоким соотношением сторон чрезвычайно сложной, если не невозможной.
Электроэрозионная обработка с малыми отверстиями также используется для создания микроскопических отверстий для компонентов топливной системы, фильер для синтетических волокон, таких как вискоза , и других применений.
Существуют также автономные электроэрозионные станки для сверления небольших отверстий с осью x – y , также известные как суперсверла или перфораторы , которые могут обрабатывать глухие или сквозные отверстия. Электроэрозионное сверление отверстий осуществляется с помощью длинного латунного или медного трубчатого электрода, который вращается в патроне с постоянным потоком дистиллированной или деионизированной воды, протекающей через электрод в качестве промывочного агента и диэлектрика. Электродные трубки работают как проволока в электроэрозионных станках, имея искровой промежуток и скорость износа. Некоторые электроэрозионные станки для сверления небольших отверстий способны просверлить 100 мм мягкой или закаленной стали менее чем за 10 секунд, при этом средний износ составляет от 50% до 80%. При таком сверлении можно получить отверстия диаметром от 0,3 мм до 6,1 мм. Латунные электроды легче обрабатывать, но их не рекомендуется использовать для резки проволоки из-за эродированных частиц латуни, вызывающих обрыв проволоки «латунь по латуни», поэтому рекомендуется использовать медь.
Механическая обработка металла [ править ]
Некоторые производители производят электроэрозионные станки специально для удаления сломанных режущих инструментов и крепежных деталей с заготовок. В этой заявке этот процесс называется «обработка дезинтеграцией металла» или MDM. В процессе распада металла удаляется только центр сломанного инструмента или крепежа, оставляя отверстие нетронутым и позволяя восстановить испорченную деталь.
Замкнутое производство [ править ]
Производство с замкнутым циклом может повысить точность и снизить затраты на инструмент.
Преимущества и недостатки [ править ]
Электроэрозионную обработку часто сравнивают с электрохимической обработкой .К преимуществам EDM относятся:
- Способность обрабатывать сложные формы, которые в противном случае было бы трудно изготовить обычными режущими инструментами.
- Обработка чрезвычайно твердых материалов с очень жесткими допусками.
- Можно обрабатывать очень маленькие детали, где обычные режущие инструменты могут повредить деталь из-за избыточного давления режущего инструмента.
- Прямого контакта между инструментом и заготовкой нет. Таким образом, деликатные участки и слабые материалы можно обрабатывать без заметной деформации.
- Можно получить хорошее качество поверхности; очень хорошую поверхность можно получить, используя дополнительные пути отделки.
- Можно получить очень мелкие отверстия.
- Могут быть изготовлены конические отверстия.
- Внутренние контуры и внутренние углы трубы или контейнера до R 0,001 дюйма.
К недостаткам EDM относятся:
- Трудности с поиском опытных машинистов.
- Медленная скорость удаления материала.
- Потенциальная опасность пожара, связанная с использованием диэлектриков на основе горючего масла.
- Дополнительное время и затраты, затраченные на создание электродов для электроэрозионной обработки с плунжером/проходцем.
- Воспроизведение острых углов на заготовке затруднено из-за износа электрода.
- Удельное энергопотребление очень велико.
- Потребление электроэнергии высокое.
- Образуется «перерез».
- В процессе обработки происходит чрезмерный износ инструмента.
- Электронепроводящие материалы можно обрабатывать только при определенной организации процесса. [32] [33]
- На поверхности реза за счет плавления материала дугой образуется релитный слой.
См. также [ править ]
Ссылки [ править ]
- ^ Джеймсон 2001 , с. 1.
- ^ Джайсвал, Вишал. «Принцип работы электроэрозионной обработки, типы, параметры процесса, оборудование и приложения» . сайт Mechanicalsite.com . Проверено 25 августа 2023 г.
- ^ Джеймсон 2001 , с. 8.
- ^ Lazarenko, B.R.; Mikhailov, V.V.; Gitlevich, A.E.; Verkhoturov, A.D.; Anfimov, I.S. "Distribution of elements in surface layers during electric spark alloying. (Raspredelenie Elementov V Poverkhnostnykh Sloyakh Pri Elektroiskrovom Legirovanii)". Surf. Eng. Appl. Electrochem. (Elektronnaya Obrabotka Materialov) . 1977, 3: 28–33.
{{cite journal}}
: CS1 maint: несколько имен: список авторов ( ссылка ) - ^ Lazarenko, B.R.; Duradzhi, V.N.; Bryantsev, I.V. "Effect of Incorporating an additional inductance on the characteristics of anode and cathode processes. (O Vliyanii Vklyucheniya Dopolnitel'noi Induktivnosti Na Kharakteristiki Anodnogo I Katodnogo Protsessov)". Surf. Eng. Appl. Electrochem. (Elektronnaya Obrabotka Materialov) . 1979, 5: 8–13.
{{cite journal}}
: CS1 maint: несколько имен: список авторов ( ссылка ) - ^ Lazarenko, B.R.; Lazarenko, N.I. "Electric spark machining of metals in water and electrolytes. (Elektroiskrovaya Obrabotka Metallov V Vode I Elektrolitakh)". Surf. Eng. Appl. Electrochem. (Elektronnaya Obrabotka Materialov) . 1980, 1: 5–8.
{{cite journal}}
: CS1 maint: несколько имен: список авторов ( ссылка ) - ^ Крар, Стивен Ф.; Гилл, Артур Р. (2003). Изучение передовых производственных технологий (1-е изд.). Промышленная пресса. п. 6.2.1. ISBN 0831131500 .
- ^ Джеймсон 2001 , стр. 10–12.
- ^ Дулебон, «Обработка с использованием трассировщика путем электроиндуцированной эрозии», патент США № 3614372 , поданный 4 декабря 1969 г., выданный 19 октября 1971 г.
- ^ Джеймсон 2001 , стр. 12–17.
- ^ Jump up to: Перейти обратно: а б с Роджерс, Барри (2018), «Замечательные возможности проволочной электроэрозионной обработки» , TechSpex , заархивировано из оригинала 22 мая 2018 г. , получено 21 мая 2018 г.
- ^ Мори, Н.; Фукузава, Ю.; Тани, Т.; Сайто, Н.; Фурутани, К. (1996). «Метод вспомогательного электрода для обработки изоляционной керамики». Анналы CIRP - Технология производства . 45 : 201–204. дои : 10.1016/S0007-8506(07)63047-9 .
- ^ Лю Ю.Х., Ли Х.П., Цзи Р.Дж., Ю.Л.Л., Чжан Х.Ф., Ли Ци (2008). «Влияние технологического параметра на производительность процесса электроэрозионного фрезерования изоляционной керамики Al2O3». Журнал технологии обработки материалов . 208 (1–3): 245–250. дои : 10.1016/j.jmatprotec.2007.12.143 .
- ^ Морган, CJ; Валланс, РР; Марш, скорая помощь (2004). «Микрообработка стекла поликристаллическими алмазными инструментами, сформированными методом микроэлектроэрозионной обработки». Журнал микромеханики и микроинженерии . 14 (12): 1687. Бибкод : 2004JMiMi..14.1687M . дои : 10.1088/0960-1317/14/12/013 . S2CID 250921623 .
- ^ Маккарти, Уиллард Дж. и МакГео, Джозеф А. «Станок» . Британская энциклопедия
- ^ Jump up to: Перейти обратно: а б с д Дескудрес, Антуан (2006). Характеристика электроэрозионной обработки плазмы . Это EPFL , № 3542.
- ^ Венг, FT; Шью, РФ; Сюй, CS (2003). «Изготовление микроэлектродов методом многоэлектродного шлифования». Журнал технологии обработки материалов . 140 (1–3): 332–334. дои : 10.1016/S0924-0136(03)00748-9 .
- ^ Нарасимхан, Дж.; Ю, З.; Раджуркар, КП (2005). «Компенсация износа инструмента и создание траектории в микро- и макроэрозионной обработке». Журнал производственных процессов . 7 : 75–82. дои : 10.1016/S1526-6125(05)70084-0 .
- ^ Кельш, Джеймс (октябрь 2009 г.). «EDM: меняющийся конкурентный расчет», Технологическое машиностроение , Общество инженеров-технологов.
- ^ Хан, Ф.; Чен, Л.; Ю, Д.; Чжоу, X. (2006). «Базовое исследование генератора импульсов для микроэлектроэрозионной обработки». Международный журнал передовых производственных технологий . 33 (5–6): 474. doi : 10.1007/s00170-006-0483-9 . S2CID 110776709 .
- ^ Jump up to: Перейти обратно: а б с д и Ферри, К.; Иванов А.; Петрелли, А. (2008). «Электрические измерения в µ-EDM» (PDF) . Журнал микромеханики и микроинженерии . 18 (8): 085007. Бибкод : 2008JMiMi..18h5007F . дои : 10.1088/0960-1317/18/8/085007 . S2CID 110495415 .
- ^ Ван Дейк, Франс (1973). Физико-математический анализ процесса электроэрозионной обработки . Кандидатская диссертация Католического университета Левена.
- ^ Jump up to: Перейти обратно: а б Дибитонто, Дэрил Д.; Юбанк, Филип Т.; Патель, Мукунд Р.; Барруфет, Мария А. (1989). «Теоретические модели процесса электроэрозионной обработки. I. Простая модель катодной эрозии». Журнал прикладной физики . 66 (9): 4095. Бибкод : 1989JAP....66.4095D . дои : 10.1063/1.343994 .
- ^ Jump up to: Перейти обратно: а б Патель, Мукунд Р.; Барруфет, Мария А.; Юбанк, Филип Т.; Дибитонто, Дэрил Д. (1989). «Теоретические модели процесса электроэрозионной обработки. II. Модель анодной эрозии». Журнал прикладной физики . 66 (9): 4104. Бибкод : 1989JAP....66.4104P . дои : 10.1063/1.343995 .
- ^ Jump up to: Перейти обратно: а б Юбанк, Филип Т.; Патель, Мукунд Р.; Барруфет, Мария А.; Бозкурт, Б. (1993). «Теоретические модели процесса электроэрозионной обработки. III. Цилиндрическая плазменная модель переменной массы». Журнал прикладной физики . 73 (11): 7900. Бибкод : 1993JAP....73.7900E . дои : 10.1063/1.353942 .
- ^ Сингх, А.; Гош, А. (1999). «Термоэлектрическая модель удаления материала при электроэрозионной обработке». Международный журнал станков и производства . 39 (4): 669. doi : 10.1016/S0890-6955(98)00047-9 .
- ^ Бильштейн, Роджер Э. (1999). Этапы пути к Сатурну: технологическая история ракеты-носителя «Аполлон/Сатурн» (NASA-SP4206) . Издательство ДИАНА. п. 145 . ISBN 9780788181863 .
- ^ Jump up to: Перейти обратно: а б с д и Джеймсон 2001 .
- ^ Семон, Г. (1975). Практическое руководство по электроэрозионной обработке. 2-е изд . Ателье де Шармиль, Женева.
- ^ Тодд, Роберт Х.; Аллен, Делл К.; Альтинг, Лео (1994). Справочное руководство по производственным процессам . Industrial Press Inc., стр. 175–179. ISBN 0-8311-3049-0 .
- ^ ЭЛЕКТРОЭРОЗДНАЯ ОБРАБОТКА (EDM) . заголовок.com
- ^ Кучуктюрк, Г.; Когун, К. (2010). «Новый метод обработки электронепроводящих заготовок методом электроэрозионной обработки». Машиностроение и технологии . 14 (2): 189. дои : 10.1080/10910344.2010.500497 . S2CID 138552270 . (2010).
- ^ Окункова Анна Александровна; Волосова Марина Александровна; Хамди, Халед; Гхашим, Хасан И. (февраль 2023 г.). «Электроэрозионная обработка глинозема с использованием одно- и многослойных покрытий Cu-Ag и Cu и водно-порошковой среды ZnO» . Технологии . 11 (1): 6. doi : 10.3390/technologies11010006 . ISSN 2227-7080 .
Библиография [ править ]
Джеймсон, ЕС (2001). Электроэрозионная обработка . МСП. ISBN 978-0-87263-521-0 . Архивировано из оригинала 28 сентября 2011 г.
Внешние ссылки [ править ]
- Новая технология обнаружения дуги для высокоэффективной электроэрозионной обработки. Архивировано 3 февраля 2019 г. на Wayback Machine.
- Инженерное проектирование электроэрозионной обработки
- Как эти невероятно тонкие разрезы делаются на YouTube, автор Стив Молд (апрель 2023 г.)